By Edward C. Myers, MSChE Project Manager, Lescure Engineers, Inc.
For full article click here.
The Kunde family wished to have their winery evaluated for energy use, to discover how much they could reduce power consumption through energy efficiency measures. In 2007, they contracted with AIM Associates, a Petaluma architectural firm, whose principal George Beeler is a recognized expert in green building practices. George teamed with Dr. John Rosenblum of Rosenblum Environmental Engineering and Ed Myers of Lescure Engineers, to perform an energy audit of the winery processes and main building. … Following the audit, an engineering analysis of the performance of the winery processes and the winery building showed how the facility could be upgraded to sustainable, renewable energy at the lowest cost.
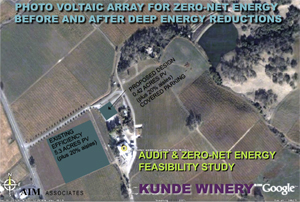 |
Administration building
|
In the twenty years since the Kunde building was designed, major improvements have been made in both the California building energy code minimum compliance and best practice design. Professional associations for architects such as the US Green Building Council and the 2030 Challenge are now promoting building designs that will use a fraction of the climate control energy needed for 1990s era buildings. A key part of this revolution in building design is the computer modeling that allows an architect to predict the energy use of a building, and test different energy efficiency improvement strategies. George Beeler used a computer model called eQUEST to simulate the energy use of the Kunde building in its present form. The model’s predicted energy use was compared to the energy use measured during the audit, to verify the computer model was working correctly. The computer model was adjusted accordingly. George then predicted the effect of building improvements such as night and economizer cooling, daylight harvesting controls (which make daylight use more efficient and pleasant), more efficient lighting and occupancy controls, solar space heating, better windows and skylights, sealing air leaks, improving insulation and more efficient heat pumps,. All these improvements were estimated to reduce building lighting, cooling, ventilation and heating energy use by 80+%.
The analyses of the winery refrigeration system and the building show that dramatic reductions in utility power purchases (and the associated greenhouse gas emissions) were possible with efficiency improvements. The next question is – at what cost, and what is the return on investment?
…This analysis indicates that the financial incentive for tank insulation is very attractive – a simple payback of less than two years. However, financial incentives alone are not as attractive for the Integrated scenario, which yields the greatest energy savings. However, if Kunde’s goal is to eliminate their GHG emissions from utility power, how do the costs and benefits of efficiency improvements compare to purchasing a solar PV system to power the entire facility?
Even before considering solar PV’s cost, how large would the solar array have to be to power the existing winery and building? This aerial photograph of the Kunde property, with two sizes of PV solar arrays shown as the overlaid green squares.
Generating the power needed by the winery and building – with no improvements in efficiency – would require over 5 acres of PV solar arrays. If producing vineyards had to be removed as shown in the picture, this would significantly impact revenue. However, with all the efficiency improvements the DesignSmart Group (AIM with Lescure) believes are possible, a much smaller solar PV array (less than half an acre) could be used, which could be placed over the existing visiting wine taster’s parking lot for shade. (The integrated design approach always looks for multiple benefits.)
For full article click here.
<···
Back to projects page
|